Industrial Automation System
- Home
- Industrial Automation System
PLC / SCADA based Main-Machine Interface
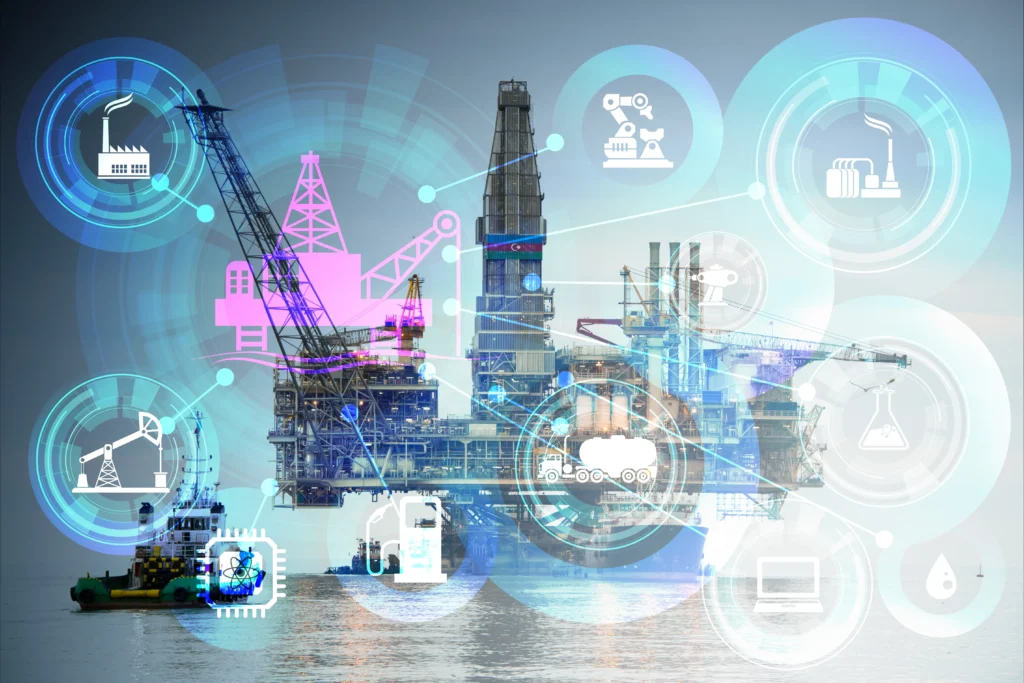
Integrating PLC and SCADA systems can provide significant benefits for industrial automation applications, combining the real-time control capabilities of PLCs with the supervisory, data acquisition, and analysis features of SCADA systems. This integration enables more efficient control and monitoring of industrial processes, as well as improved decision-making and process optimization.
By integrating PLC and SCADA systems, control and monitoring functions are enhanced, enabling more efficient and effective management of industrial processes. Operators can monitor the status of devices and processes in real-time, detect anomalies, and make informed decisions based on the collected data.
Direct Digital Logical Controller(DDC) based Interface – Real time monitoring System
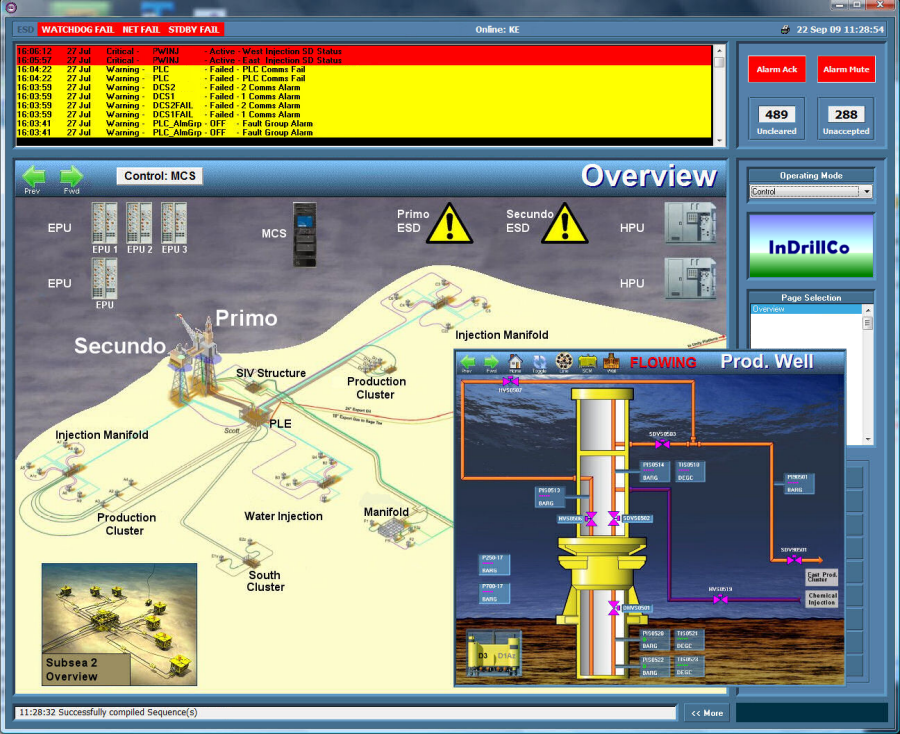
DDC systems control a building’s conditions through a central computer that monitors performance. DDC systems monitor functions, such as temperature and lighting via sensors and output signals, such as to control valves, open doors, and sound alarms.
A building automation system (BAS) uses a DDC system to automate the control of various building systems. DDC and BAS work together to provide programmable and precise control of a building’s functions, increasing a building’s energy efficiency and warning when a system is at risk. The DDC system that controls a commercial HVAC system may also control other building systems, such as mechanical and electrical systems, to automate the entire building.
Overall, DDC systems and automation offer control over a building’s functions and can help increase a building’s comfort levels while reducing its energy consumption.
Vapor recovery system (VRU)
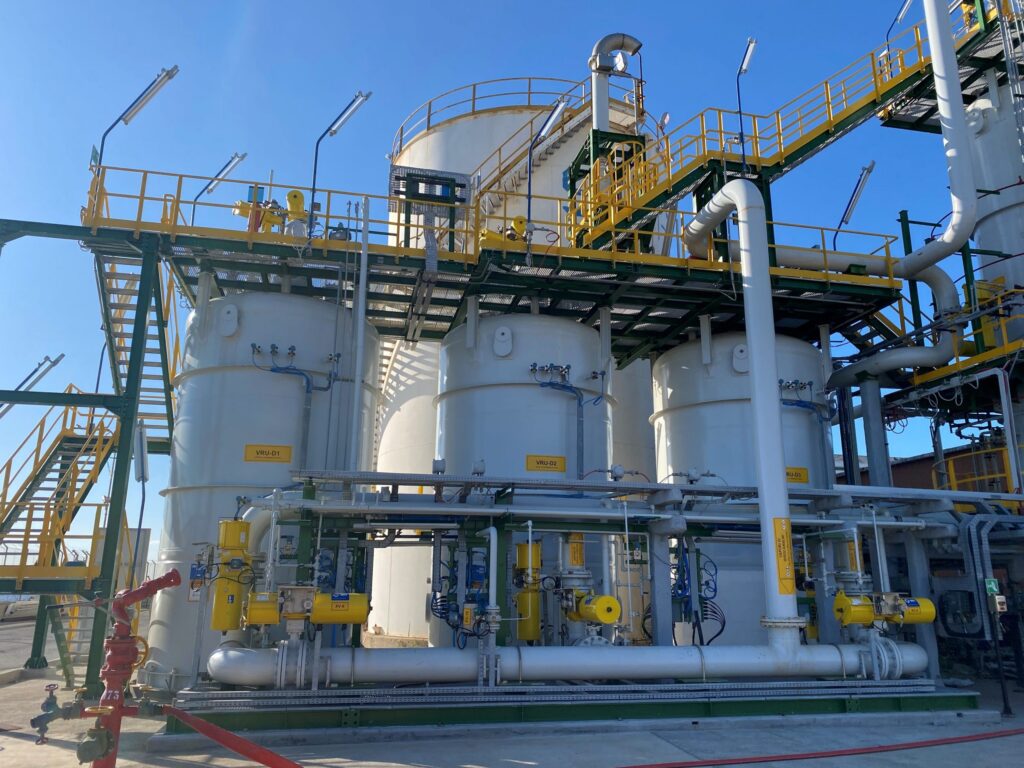
A Vapor Recovery Unit (VRU) is a set-up designed to remove unwanted vapors present in crude oil or distillate tanks allowing operators to comply with prevailing emission regulations. VRU systems can be employed in a wide range of chemical industries with several variants available. For example, a vapor recovery system for storage tanks can be used to recover vent gas from crude oil and distillate tanks at storage facilities.
VRUs are mechanically driven and are powered by an electric motor or gas engine depending on what’s available. The VRU working principle is based on the Ideal gas law (PV = nRT or pressure x volume = gas mass x temperature x gas constant). In essence, when you compact your process gas into a smaller volume, the pressure of the gas increases.
The typical VRU consists of four principal components:
- Gas Compressor
- Scrubber
- Variable Frequency Drives (VFDs)
- Switching device
Valve stations
- Valve stations are part of a piping system that controls the flow and pressure of the contents it carries. It acts as a control system and is built along the pipeline above the right-of-way such as near roads, away from overhead electric lines and other obstructions. Valve stations are placed in such a way that workers can get quick access in case of an emergency.
- Valve stations can be remotely operated, and a communication system is used to interact between all valve stations in a system. With the help of these stations, it is possible to isolate a particular segment of the pipeline for maintenance or repair work. Depending on the type of pipeline, i.e., the type of product the pipeline transports, the valve stations are located at intervals of 20 to 30 miles.
Chemical injection/Dosing skids
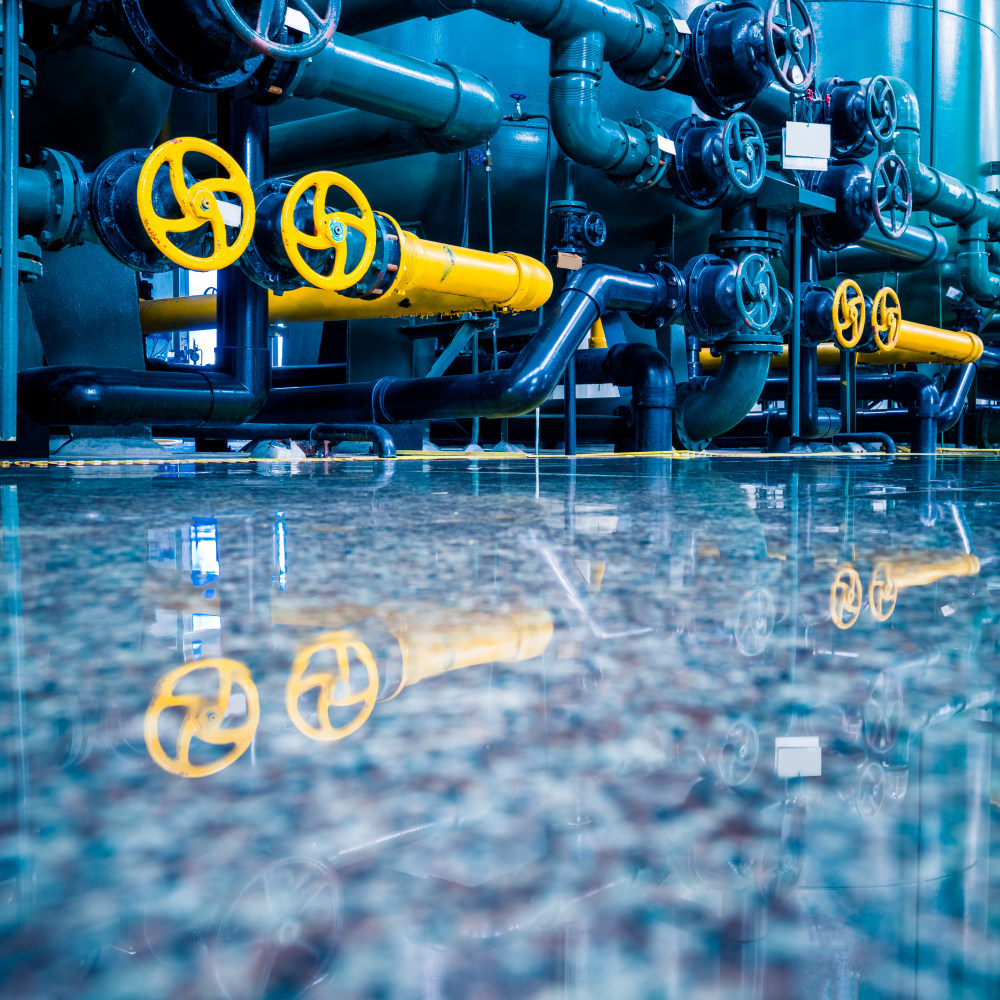
Chemical Injection Skid, as the name implies, is a piece of equipment designed to inject chemicals into a system at the required pressure for the system.
Chemical injection may function continuously or intermittently, and it can be used in a wide range of settings for many different purposes in marine and offshore industry.
Through this kind of oil industry system, water is injected into the reservoir to increase pressure and stimulate the production. It is also used to displace or sweep the oil from the reservoir, pushing it towards water injection wells which are usually found in both onshore and offshore. Only 30% of the oil in a reservoir is extracted so the system is needed to increase that percentage and maintain the reservoir’s rate of production for a long period of time.
Gas pressure reducing skids
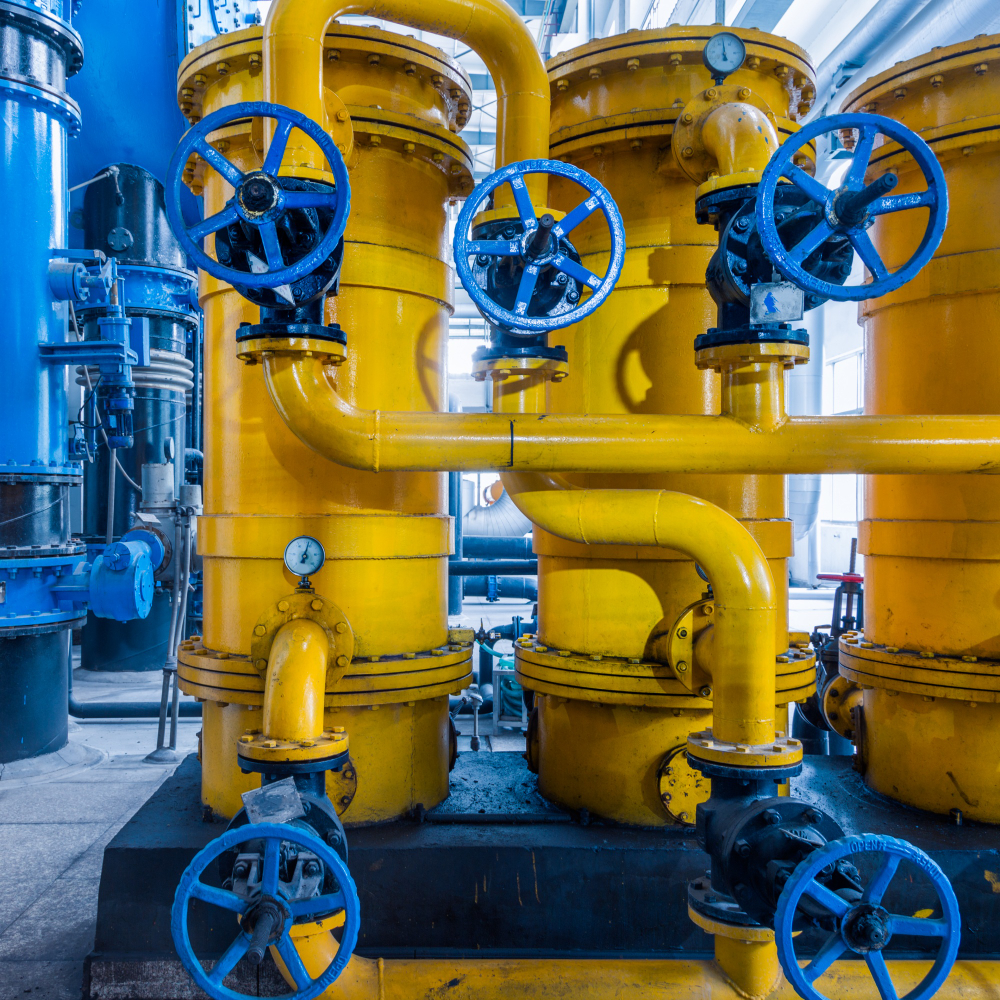
Pressure reduction stations are required to regulate the high incoming pipeline pressure to meet the desired equipment pressure. Plants utilize equipment such as gas compressors, engines, turbines, burners, etc. have a demand of a specific operating pressure range set by the equipment manufacturer.
Gas metering skids
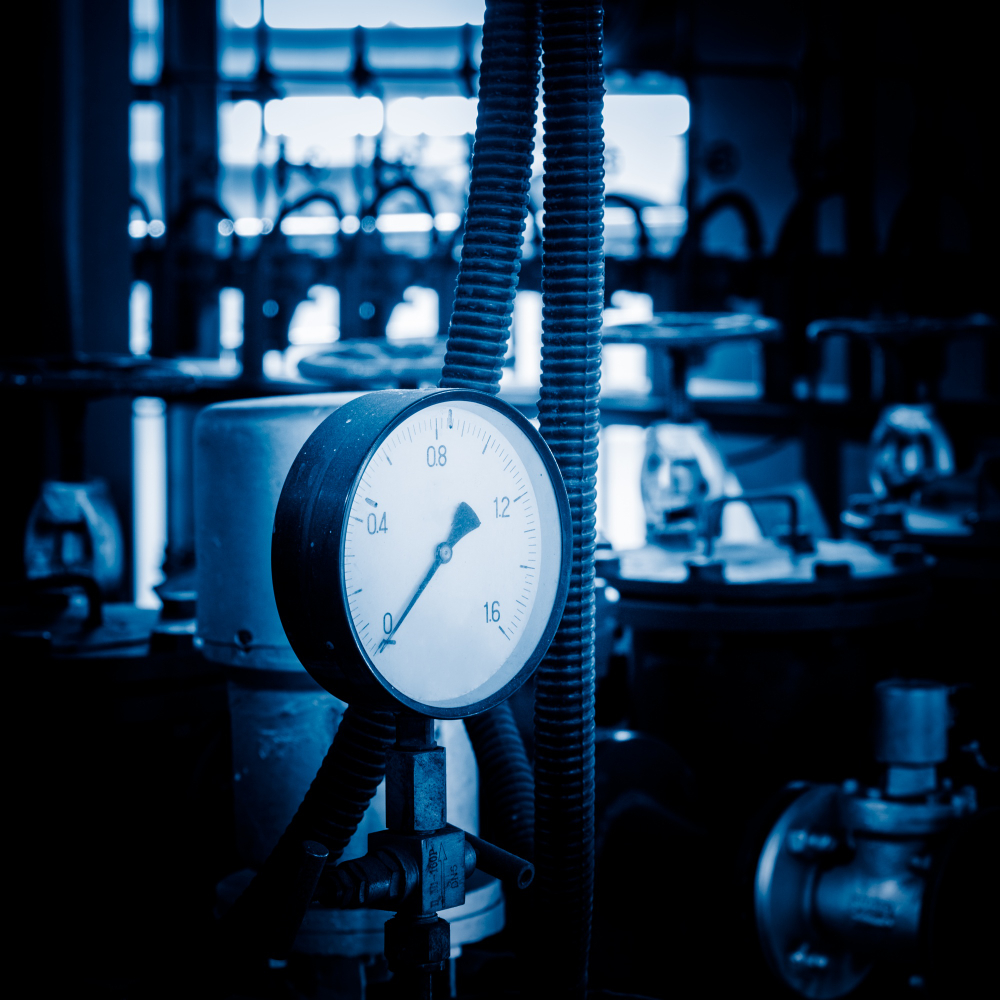
A Gas Meter Skid is a pre-packaged system used to measure and regulate the flow of gases in the hydrocarbon industry. The key components of a Gas Meter Skid typically include: Inlet and Outlet Connections are the entry and exit points for the gas to flow into and out of the skid.
Automatic control of all utility function
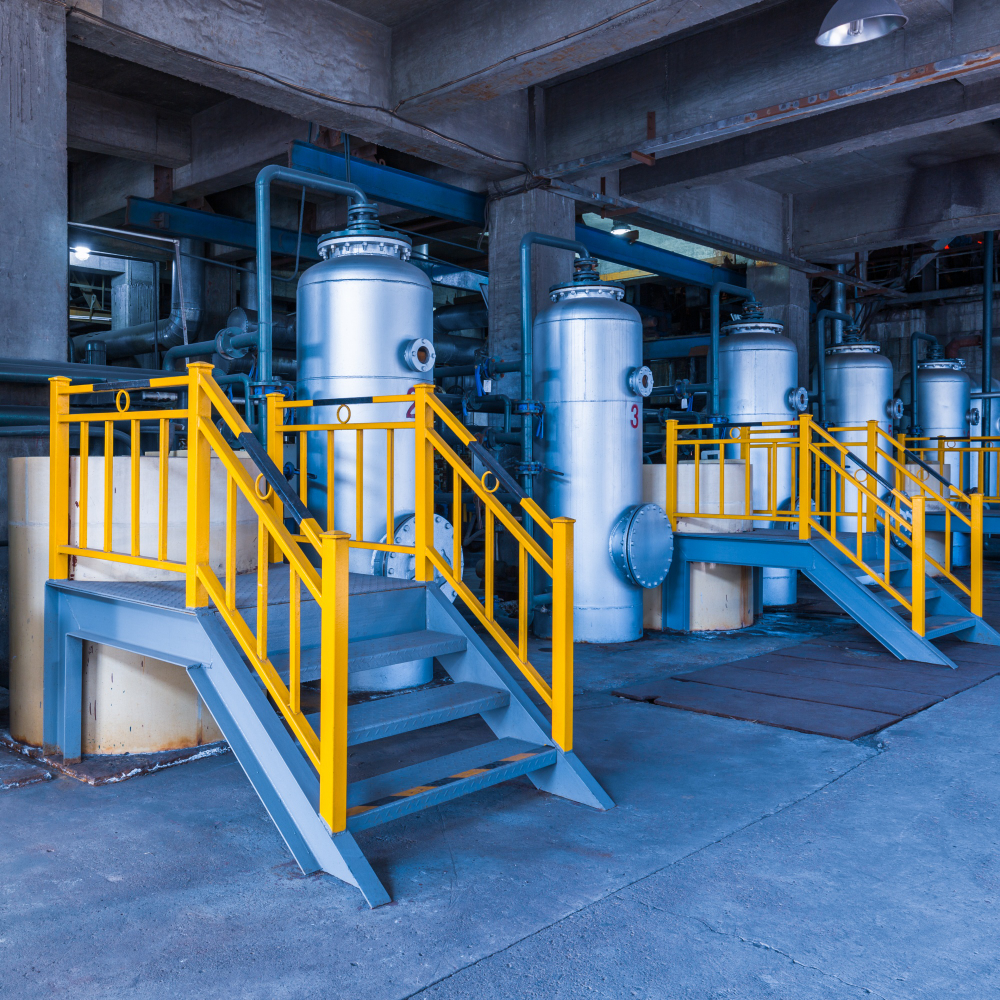
Technology that is widely used in the utilities industry to monitor and control various aspects of the power grid, such as electricity generation, transmission, and distribution. The future of SCADA in the utilities industry is expected to be driven by a number of trends, including increased automation, advanced analytics, and the integration of renewable energy sources.